CUSTOMER: SE Laboratories
SE Laboratories Test Automation
PROJECT OBJECTIVE: (in General)
The customer, SE Laboratories, provides equipment and instrumentation calibration services and needed a way to automate the control of a very complex Tektronix TDS series oscilloscope, (TDS7104A). Their testing required them to setup very specific windows and conditions that would define the portion of a signal that they would capture. To make this more complex they
wanted the scope to conditional be configured based upon other measurements it had taken in previous captures. This was to provide calculated limits based upon the standard they were testing against. They also wanted to the scope to display info about the Asset being tested, applicable regulatory standard, and other parameters during testing. This was all then to be captured. The scope Tektronix scope in this case provided a means to control almost every aspect of the capture and display via GPIB/SCPI interface.
CUSTOMERS’ STATED OBJECTIVES FOR PROJECT:
To build software driven platform that will allow a calibration technician do the following:
Control Tektronix TDS series oscilloscope
♦ Send predefined setup configuration(s) to TDS7104A
♦ Send Screen Text to TDS7104A (Asset Number, applicable regulatory standard, and other parameters specific to test)
♦ Provide selection mechanism to allow selection of predefined 'canned’ text (txt or xml) and sending to oscilloscope
♦ Collect Data from TDS series oscilloscope
♦ Download and aggregate all reported data from TDS7104A for analysis
♦ Download Screen Waveform (in Color)
Data Analysis 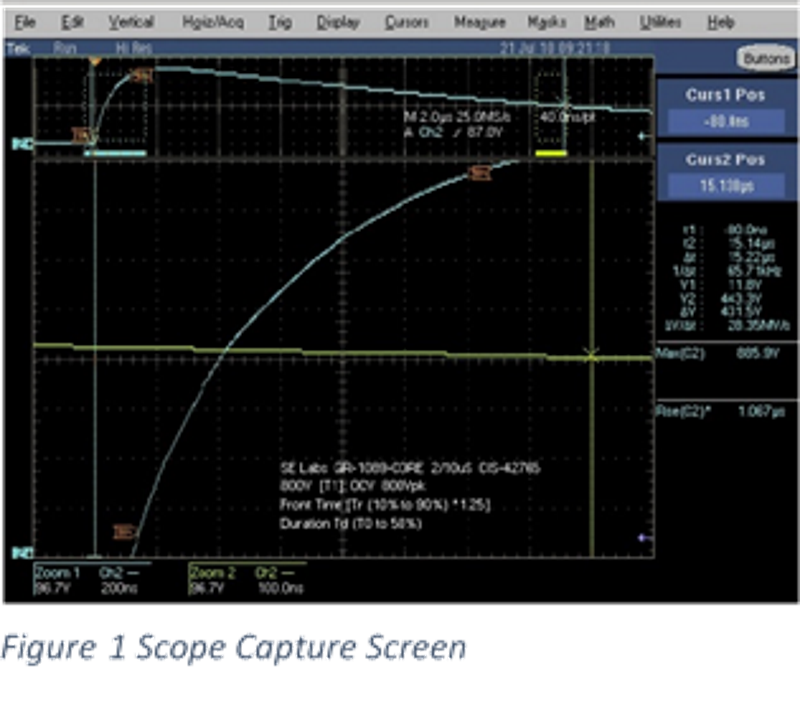
♦ Calculations made upon measured data to determine if unit is within specifications.
Save Capture Data
♦ Save parametric data captured from TDS7104A in manageable data format (Excel, xml)
♦ Save Screen Waveform (in color) as .jpg file.
♦ Save Waveforms in folder reflecting asset number
♦ Sequential Waveform captures will be named as such (01.jpg, 02.jpg etc.)
DEVELOPED:
Ashford Solutions developed a LabVIEW control application that fully configured and operated the TDS7104A Scope throughout the test sequence with little to no operator intervention other than setup and configuration of the device under test.
The test program loaded test scripts and configuration files that defined every aspect of the test and the various standards that applied and would be later used by the test to highlight ‘on screen’ out-of-spec test results when they occurred.
The application program was quite extensible and because it was table driven could be altered as the standards changed without having to change the program itself.
CHALLENGES:
Development of this application posed several complicated challenges. We had to become intimately familiar with and control of various functions of both this oscilloscope as well as the customers test system and complex test metrics.